- Important short notes for Industry and Regulators - November 3, 2024
- Remifentanil: A Powerful Pain Medication - June 29, 2024
- Requirements for License for Repacking of Drugs: Key points - May 24, 2024
Last Updated on March 13, 2024 by The Health Master
Schedule M
In the intricate realm of pharmaceuticals, compliance with regulatory standards is paramount. One such critical document that serves as a guiding light for both regulators and pharmaceutical manufacturers is Schedule M.
This article delves into the essence of Schedule M, comprising 31 chapters that lay down the foundation for ensuring the quality, safety, and efficacy of pharmaceutical products.
Key highlights of 31 Chapters on Schedule M
1. Building:

- Implement SOPs for pest control and ensure meticulous maintenance of records.
- Design the walls and floor for easy cleaning purposes.
- Regularly inspect the building for any cracks.
- Ensure that Air Handling Units (AHUs) are regularly checked and maintained in good working condition.
- Conduct regular monitoring of pressure differentials and temperature in the Raw Material (RM) area.
- Install GMP-compliant doors.
- Establish an SOP for monitoring Lux levels and maintain Lux levels consistently.
- Consider air-conditioning for the packing area.
- Equip the production area with AHUs.
- Provide air-conditioning in the warehouse.
- Implement air-conditioning in the QC area.
- Install GMP-compliant drains in the production area.
- Maintain sanitization records for drains in the production area.
Download PDF of Gist of 31 Chapters on Schedule M, link is given below the article
2. Ancillary areas:
- Ensure that rest and refreshment rooms are separated and do not lead directly to the manufacturing and warehouse areas.
- Provide accessible and well-maintained toilets.
- Supply aprons to all staff members.
- Establish an SOP for washing clothes, and maintain comprehensive records.
- Ensure the availability of two changing rooms, designated for male and female staff members.
- Designate a dedicated area for a maintenance workshop within the facility.
3. Check list:

- Ensure that product specifications align with the information on the labels.
- Adhere to the sale of drugs in accordance with the Drug Price Control Order (DPCO) 2013 regulations.
- Retain reference standards for all drugs manufactured by the firm.
- Obtain a No Objection Certificate (NOC) from the fire department.
- Obtain an NOC from the pollution control authority.
- Maintain medical records for all staff members.
- Keep a record of Form 51.
- Maintain two stability chambers.
- Upload the necessary data under Rule 84AB.
- Keep records of validation activities.
- Maintain calibrated equipment records.
- Develop and maintain a site master file.
- Conduct periodic self-inspections.
- Keep a record of control samples.
- Document records of customer complaints.
- Record information on substandard samples.
- Retain water test reports.
- Record the AHU numbers.
- Document a list of impurities.
- Maintain a list of machines.
- Keep a record of instruments.
- Document a list of directors.
- Maintain a list of technical staff.
- Keep a record of approved technical staff.
- Maintain a list of Standard Operating Procedures (SOPs).
- Keep a record of all certificates.
- Retain all manufacturing and testing records.
- Document pest control activities.
4. Self-inspection:
- Consider implementing an SOP for self-inspections.
- Suggest having Quality Assurance (QA) take charge of the control process.
- Recommend generating inspection reports in accordance with the SOP.
- Ensure that all reports clearly demonstrate compliance with their respective requirements.
- It is advisable to define the qualifications of trainers in the SOP.
- Encourage conducting yearly inspections.
- Consider including individuals from other departments in the inspection team.
5. Disposal of Sewage:
- Ensure that an NOC is obtained from the State Pollution Control Board. Confirm the operational status of the Effluent Treatment Plant (ETP).
- It is recommended to maintain Standard Operating Procedures (SOPs) for disposal.
- Consider establishing an agreement with a company for bio-disposal to enhance the firm’s waste management practices.
6. Health, clothing and sanitation of workers:
- Ensure that comprehensive medical records, including eye examinations, tuberculosis screenings, and assessments for skin and communicable contagious diseases, are regularly submitted for all staff.
- It is recommended to maintain and regularly update Standard Operating Procedures (SOPs).
- Consider establishing an agreement with a qualified medical practitioner.
- It is advisable to maintain investigational reports, including X-rays, as part of the record-keeping process.
- Encourage the reporting of staff illnesses, with a systematic maintenance of corresponding records.
- Confirm that there are no reports of individuals being restricted from entering the production area.
- Regularly monitor manufacturing areas to ensure the absence of unhygienic practices.
- Emphasize personnel training to uphold a high standard of personal hygiene, with the maintenance of associated SOPs.
- Provide a crossover bench in the change room for enhanced hygiene practices.
- Supply slippers to be worn inside the factory for the convenience and cleanliness of staff.
7. Training:
- Ensure that staff training includes the presentation of SOPs, and maintain detailed records of the training sessions.
- Provide job duty-related training to all personnel during induction, and ensure the maintenance of SOPs for reference.
8. Warehousing Area:
- Ensure proper organization and maintenance in the following areas:
- Warehousing of raw materials.
- Packaging materials.
- Quarantine.
- Finished products.
- Rejected or returned materials.
- Additionally, establish a material receiving and dispatching bay equipped with an air curtain.
- Maintain cleanliness, dry conditions, and adherence to specified temperature limits in the designated area.
- Provide suitable storage arrangements for materials sensitive to temperature, humidity, and light, and diligently maintain records.
- Safeguard receiving and dispatch bays to protect incoming and outgoing materials.
- Treat and clean incoming materials before entry into the plant, with the provision of a designated dusting area. Maintain records of these activities.
- Segregate quarantined materials from others, and restrict entry to the quarantined area.
- Store passed raw materials in a separate room, utilizing racks, bins, and platforms.
- Establish a designated area for primary packaging materials (PPM) storage, affix status labels (approved, under test, return), and maintain temperature control in the PPM area.
- Dedicate an area for the sampling of primary packaging materials (PVC).
- Allocate a distinct area for the storage of rejected, recalled, or returned materials, restricting access to this area.
- Store secondary packaging materials securely and separately.
- Provide separate storage for printed secondary packaging materials.
- Store printed packaging materials, product leaflets, etc., separately to prevent mix-ups.
- Designate an area for labels, cartons, boxes, circulars, inserts, and leaflets, ensuring proper control.
- Maintain records of the receipt of all labeling and packaging materials.
- Dispose of unused packaging materials returned to the store and maintain records.
- Control returned/unused packaging materials, such as foils, and maintain records.
- Install Laminar Air Flow units (LAFs) with HEPA filters in the dispensing and sampling area, monitoring pressure differentials with pressure gauges in the LAFs. Provide a logbook for the sampling booth.
- Conduct dispensing in accordance with the current SOP.
- Keep dispensed materials for each batch of the final product together and clearly labeled.
- Implement an SOP for handling spillage, breakage, and leakage of containers.
- Handle and store narcotics and psychotropic drugs separately.
9. Raw Materials:
- It is recommended to develop an SOP for the receiving and processing of incoming materials.
- Consider adopting the “First In, First Out” or “First Expiry” principle, and ensure the maintenance of the SOP.
- Apply fixed labels on all raw materials for clarity and consistency.
- Ensure that all materials are purchased from approved vendors and provide the approved vendor list along with raw materials. Maintain the SOP.
- Establish a practice of identifying and recording damaged containers.
- Implement a comprehensive sampling, testing, and release process for each batch of raw materials. Include testing for drums, unopened containers, Gelatin Capsule Shells, complete testing of Starch, and pathogen tests.
- Ensure that raw materials in the storage area include information such as the designated name of the product, internal code reference, analytical reference number, manufacturer’s name, address, batch number, status of contents (e.g., quarantine, under test, released, approved, rejected), and manufacturing date, expiry date, and retest date.
- Attach a fixed label indicating “Under Test” on containers from which samples have been drawn.
- Consider conducting the following actions:
- Complete testing as per IP monograph.
- Conduct identification tests (IR) and RS tests.
- Maintain raw data records.
- Keep HPLC data records.
- Release drugs after thorough testing, duly signed by staff.
10. General:
- Ensure a proper flow of materials and personnel within the facility.
- Consider installing a pass box in the manufacturing area to facilitate the movement of materials.
- Design and install premises and equipment in a manner that facilitates effective cleaning and decontamination.
- Store all stripes in a designated and separate room.
- Prepare coating solutions under controlled conditions to ensure quality and consistency.
- Clearly identify all service lines, indicating the direction of flow, and implement color coding for easy recognition.
11. Air Handling Systems (HVAC):
- Regularly maintain dust collectors within the facility.
- Install a pressure gauge to monitor pressure differentials effectively.
- Implement temperature monitoring for the Raw Material (RM) core area.
12. Manufacturing Operations and Controls:
- Label containers with the product name, batch number, batch size, and stage of manufacture, accompanied by the signature of the technical staff.
- Ensure that products not prepared under aseptic conditions are free from pathogens such as Salmonella, Escherichia coli, and Pyocyanea. The firm has a microbial laboratory for pathogen testing and maintains corresponding records.
- Maintain the microbiology laboratory.
13. Precautions against mix-up and cross-contaminations:
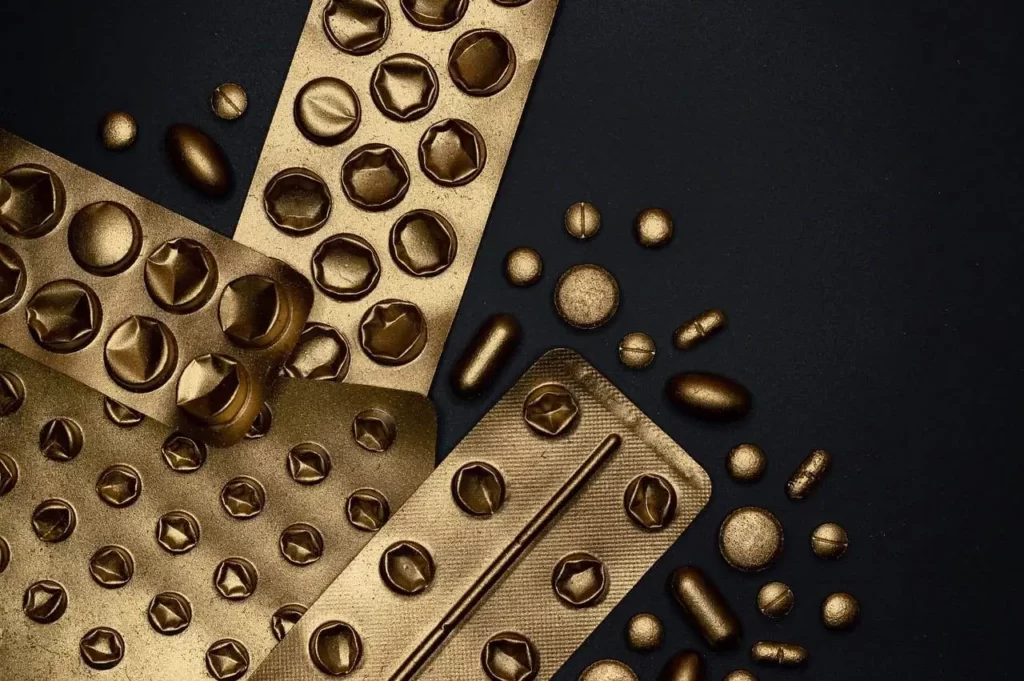
- The firm must install appropriate Air Handling Units (AHUs), and validation confirms that all AHUs are in working order.
- Dust collectors to be strategically provided in different sections.
- Separate entry points for personnel and materials are established within the facility.
- Pressure gauges are in place to monitor pressure differentials in the production area.
- SOPs must be implemented to prevent mix-ups during various stages of production.
- Equipment used for production is appropriately labeled with its current status.
- Conduct line clearance procedures, and maintain records of the clearance activities.
- Establish a dedicated area for carton coding.
- Authorized personnel are permitted entry.
- Follow separate gowning procedures before entering core areas.
- Implement a door interlocking facility for added security.
- Provide SOPs to verify the effectiveness of measures preventing cross-contamination.
14. Sanitation in the Manufacturing Areas:
- Ensure that cleaning procedures in the manufacturing areas align with the Standard Operating Procedures (SOPs), and maintain thorough records.
- Validate cleaning procedures to ensure their effectiveness.
- Conduct routine sanitation, following the corresponding SOPs, and maintain proper records of these activities.
- Ensure adequate lighting in the production area.
- Record observed lux levels in production, conduct regular visual inspections, and maintain detailed records of these observations.
- Provide comprehensive procedures for product changeovers in accordance with the SOPs.
15. Equipment:
- Ensure that the equipment is both clean and well-maintained.
- Provide log books for all equipment, presented in a bind format.
- Adhere to the SOP for cleaning equipment after each batch, as outlined in the procedures.
- Conduct cleaning hold time and dirty equipment hold time studies, as carried out by the firm.
- Allocate a separate area for the storage of machine parts and other equipment components.
- Ensure that balances and other measuring equipment, with appropriate ranges, are available in Raw Material stores and production areas. Calibrate them in accordance with the maintained SOP.
- Maintain records specifying the material of construction for contact parts of production equipment.
- Confirm the use of Food grade lubricants by the firm, and provide a Certificate of Analysis (COA) for verification.
- Submit procedures for the removal of defective equipment from production areas, and ensure that the corresponding SOP is maintained.
16. Documentation and Records:
- Ensure accurate completion of all daily documents, including the Batch Production Record (BPR).
- The firm has implemented a policy for creating an audit trail when issuing documents.
- Documents must be approved, signed, and dated by the relevant and authorized personnel.
17. Labels:
- Verify that labels are printed in a legible manner.
- Confirm that label artwork has been approved in accordance with the specified requirements.
- Assure that labels adhere to the requirements outlined in Rule 96, Rule 97, and other pertinent provisions.
18. Master Formula Records:
- Establish, authorize, and control master formula records for each product.
- Ensure that the master formula is specific to the batch size.
19. Packaging area and its record :
- Maintain authorized packaging instructions for each product, accounting for various pack sizes and types.
- Label all materials, equipment, rooms, and packaging lines with an indication of the processed product and the corresponding batch number.
- Ensure that packaging lines are independent and adequate.
- Adhere to the SOP for line clearance, and maintain records accordingly.
- Transport packaging materials on covered trolleys upon arrival.
- Verify quantities of packaging materials against the amounts dispensed from the warehouse.
- Calculate batch yield immediately after completing the packaging operation and before introducing a new batch.
- Dispose of excess printed packaging material upon completing the batch.
- Designate a separate area for printed packaging material awaiting destruction.
- Ensure that the Batch Packaging Record includes all points prescribed in Schedule ‘M’.
- Attach all documents generated during packaging to the Batch Packaging Record.
- Base the Batch Packaging Record on the current master formula record.
20. Standard Operating Procedures and Records:
- Maintain a list of Standard Operating Procedures (SOPs).
- Display SOPs in designated areas.
- Ensure proper formatting of SOPs for clarity and effectiveness.
21. Reprocessing and Recoveries:
- Adhere to the Standard Operating Procedure (SOP) for reprocessing.
- Add recoveries into subsequent batches in accordance with the SOP.
22. Finished Product:
- Place finished products in quarantine until they receive final release from the Quality Assurance (QA) department.
- The company maintains a dedicated finished goods (FG) store.
23. Quality Control Area:

- The Quality Control (QC) area is distinct from the production area.
- It encompasses instrumentation, a chemical lab, and a microbial lab.
- Material testing is carried out in accordance with the Standard Operating Procedure (SOP).
- The company has provided electronic balances that are safeguarded from vibrations, electrical interference, and humidity.
- Conduct annual calibration of standard weights and daily calibrations of all weighing balances.
- Install a fuming hood and an eye shower for safety measures.
- Maintain training records, maintenance logs, and logbooks for documentation.
- Establish a washing and drying area in the chemical lab specifically for glassware.
- Utilize certified/calibrated glassware for assay procedures, and provide certificates and calibration records.
- If the firm has outsourced lab testing, submit the agreement that has been established.
- Submit a comprehensive list of equipment used in the testing processes.
- Create SOPs and maintain records for various aspects, including starting materials, primary packaging materials, secondary packaging materials, in-process materials, finished products, water analysis, wash water analysis, swab analysis, and wash water analysis of cleaned garments containers.
- Approve specifications based on validation for starting materials, primary packaging materials, secondary packaging materials, in-process materials, finished products, water analysis, wash water analysis, swab analysis, and wash water analysis of cleaned garments.
- Designate a responsible person for receiving samples for testing.
- Follow procedures for receiving and recording samples as per SOP, and maintain detailed records.
- Implement procedures for the storage and distribution of received samples to different analysts, following SOPs, and maintain records.
- Follow procedures for the preparation, consumption, and destruction of volumetric solutions according to SOPs, with records being maintained.
- Maintain a logbook for the preparation of reagents, documenting the analyst’s name, reagent name, calculations, date of preparation, and expiration, as per SOP.
- Implement procedures for using GR, LR, and AR grade chemicals/solvents for calibration and sample testing, following SOP, and maintain records.
- Follow SOPs for reporting analysis results by analysts to the QC Head, and maintain records.
- Follow procedures for the storage of samples after testing, following SOP, and maintain records.
- Implement procedures for the safe removal of waste from the laboratory.
24. Laboratory:
- Acquire reference standards from approved sources, and submit a list of these standards.
- Obtain reference standards for all drugs manufactured in the factory.
- Store reference standards in appropriate storage conditions.
- Establish Standard Operating Procedures (SOPs) for preparing working standards from reference standards.
- Develop SOPs and maintain records for both the preparation and destruction of unused working standards.
25. Microbiology Lab:
- Install separate Air Handling Units (AHUs) for microbiological testing areas.
- Submit the layout of the microbiology lab for review.
- Establish entry to the sterile area through three airlock systems with separate exits.
- Provide a list detailing the equipment used in the microbiological lab.
- Ensure operators are trained in gowning procedures, and submit training records for verification.
- Maintain pressure differences in all rooms, and keep detailed records.
- Develop and document a cleaning and disinfection program for the lab.
- Install a Laminar Air Flow (LAF) system in the sterile area.
- Provide a double-door autoclave for transferring materials from the unclassified area to the sterile area.
- Submit qualification documents for major equipment such as autoclave, incubator, hot air oven, refrigerator, and LAF.
- Routinely calibrate the temperature of the autoclave and incubator.
- Adhere to SOPs for the proper handling and disposal of chemical and microbial waste.
- Establish a procurement system for reference cultures and their maintenance.
- Define air grades for the Sterility testing room, Microbiological Assay room, MLT room, and Airlocks (entry and exit).
- Maintain records including a logbook for entry/exit in the sterile area, media preparation records, records for water testing (micro), and records for MLT.
- Provide a dedicated microbiology lab for Microbial Limit Tests (MLT) on non-sterile dosage forms.
26. Stability Studies:
- Install two stability chambers in a dedicated room.
- Ensure the maintenance of all records.
- Keep and maintain all logbooks.
- Verify that records correspond with the samples stored in stability chambers.
- Conduct both real-time and accelerated stability tests.
- Determine the expiry date of drugs based on stability data.
27. Quality Assurance:
- QA has actively participated in the following tasks:
- Development of SOPs.
- Preparation of BMR/BPR.
- Designing of formats.
- Maintenance of calibration records.
- Documentation of qualification records.
- The company has established a QA team with assigned responsibilities.
- The QA department is tasked with the implementation of all SOPs.
- The QA department is responsible for releasing finished goods.
28. Product Recall:
- The company has established a Standard Operating Procedure (SOP) for the product recall system.
- Protocols have been adhered to in handling the recalled products.
- Distribution records are accessible.
- The SOP provides clear definitions of responsibilities, procedures, and reporting.
29. Complaints and Adverse Reactions:
- Keep a Complaints Register within the firm to record all complaints.
- Develop an SOP specifically for handling complaints.
- Ensure meticulous maintenance of records.
- Incorporate a review system for handling complaints as outlined in the SOP.
30. Validation:
- Assign the responsibility of implementing it to the QA department.
- The firm has an established SOP for Validation.
- Clarify whether critical processes are validated prospectively, retrospectively, or concurrently.
- Ensure the maintenance of all validation records.
- The firm has to conduct cleaning validation.
31. Site Master File:
- Ensure that all pertinent information is incorporated into the site master file.
- Include the quality policy in the site master file.
- Prepare the site master file in accordance with Schedule M.
By
Lalit Kr. Goel, DSDC, FDA Haryana
Rakesh Dahiya, SDCO, FDA Haryana
For informative videos by The Health Master, click on the below YouTube icon:
For informative videos on Medical Store / Pharmacy, click on the below YouTube icon:
For informative videos on the news regarding Pharma / Medical Devices / Cosmetics / Homoeopathy etc., click on the below YouTube icon:
For informative videos on consumer awareness, click on the below YouTube icon: